PRODUCTION STATISTICS
Annual worldwide production / consumption of beryllium in 2014 is estimated as 300 MT:
​
​
​
​
​
​
​
​
The total supplied quantity of beryllium, converted and sold as commercial products (i.e. pure, alloy and Be contained in BeO ceramics), is estimated at 30,2 MT for the major European countries in 2011:
​
​
​
​
​
​
​
​
Beryllium annual consumption is expected to grow to 425 MT / year by 2020 and to >450 MT/year by 2030, driven by such applications as the construction of the ITER fusion reactor.​
-
The price of beryllium is dependent on the form.
-
As a fully machined aerospace component of pure beryllium: €300 – 1,500/kg
-
As a cast aluminium 39% beryllium alloy aerospace component: €200 – €500/kg
-
As a copper 2% beryllium alloy in bulk form: €20 – 50 /kg
-
As a copper 2% beryllium alloy in strip form: €20 – 50 /kg
-
As a copper 0.3% beryllium alloy in strip form: €12 – 20 /kg
-


PROPERTIES & METALLURGY
Beryllium is the fourth element on the periodic table
​
It is the 44th most abundant element in the earth’s crust
​
Beryllium is one of the lightest metals, at two-thirds the density of aluminium
​
Beryllium has six times the specific stiffness of steel
HISTORICAL PERSPECTIVE
When compared to the ancient origins of metals such as gold, copper and lead, beryllium is a relative newcomer. Though beryllium was discovered in the late 18th century, its unique properties and commercial value were not recognised until the 1920s.
​
1798 French chemist Louis-Nicholas Vauquelin discovered beryllium when he identified beryllium oxide in beryl. He
named it glucinium, because it tasted sweet like glucose (sugar).
​
1828 Elemental (metallic) beryllium was isolated in 1828 by two chemists, working independently: Antoine Bussy (France)
and Friedrich Wöhler (Germany).
​
1920s Copper beryllium alloys were first patented and used as the conductive spring components of telephone
switchboard relays produced in Germany.
​
1930s Pure beryllium is first commercialised for use in medical x-ray windows, while beryllia ceramics found application
insulating circuitry in radio tubes.
​
1940s Beryllium’s qualities supported national defence in World War II: in marine diesel engines (corrosion resistance); in
parachute buckles (strong and lightweight); and in high precision aircraft gyroscopic navigation and targeting
instruments (lightweight, stiff, non-magnetic, and dimensional stability over a wide temperature range). U.S.
government scientists discovered that pure beryllium moderates neutrons, making it ideal for control of nuclear
reactions and the function of nuclear weapons.
​
1950s Demand for beryllium and beryllium-containing materials grew rapidly in postwar markets for telecommunications,
appliances, automotive components and plastic mold tooling. The build up of strategic deterrent weapons systems
during the Cold War increased U.S. government demand for pure beryllium. With the advent of space flight in the
same era, beryllium answered the call for a light material with dimensional stability over extreme temperature
ranges.
1960s Beryllium came into its own as an essential structural material for space exploration and high-technology defence
applications. A beryllium heat shield protected NASA’s Mercury capsule and its astronaut on the first manned
journey to space. A unit of Brush Engineered Materials Inc., the industry leader, opened a bertrandite ore mine in
Utah, ensuring a secure U.S. source of beryllium.
​
1970s Beryllium materials were used extensively in the U.S. space effort, as well as in military aircraft navigation, targeting
and missile defense systems. Copper beryllium became more prevalent in the automotive electronics and
mainframe computer industries. Personal computers and mobile telephones employed beryllium’s unique electrical
and thermal properties to achieve new advances in reliability, affordability, performance and miniaturisation.
​
1980s First undersea fiberoptic telecommunication cable enters intercontinental service with copper beryllium alloy
pressure housings.
​
1990s Beryllium applications continued to shift from aerospace and defense to the automotive electronics,
telecommunications, computers and energy exploration. New beryllium materials, including aluminum beryllium
metal matrix composites, set new standards for performance. Nickel beryllium alloys enable the first inertial airbag
crash sensor systems to be deployed in automobiles, paving the way for this life-saving technology to be standard
equipment in vehicles worldwide.
​
2000s Optical-grade beryllium was selected as the primary mirror material for NASA’s James Webb Space Telescope,
scheduled to replace the Hubble Telescope in 2014. The U.S. Department of Defense cited high-purity beryllium as
the nation’s only “critical” strategic material. Beryllium materials enabled clean energy technologies from
advanced solar electric cells to nuclear fusion in experimental reactors. The European Commission lists beryllium as
one of the 34 critical materials for the European Union in its list of Critical Raw Materials.
SOURCES OF BERYLLIUM
Beryllium occurs naturally in the earth’s crust and in the air, soil and water. Every day, people are exposed naturally to extremely small amounts of beryllium by breathing the air, drinking water and eating food grown in soil.
​
Beryllium is also introduced into our lives through human activities. Here, the material typically ends up in a solid form that is designed into and contained within consumer or industrial products — everything from portable electronics to cell phones to industrial machinery to medical devices. In virtually all human-generated end-use applications, beryllium is enclosed within products and is not readily exposed to, or accessible to, people. In these enclosed forms, beryllium poses no special health risks.
BERYLLIUM EXTRACTION
Beryllium is usually obtained from two naturally occurring sources
​
The commercial extraction of beryllium begins with the mining of raw materials. The vast majority, over 95%, is obtained by mining minerals containing between 0.3 – 1.5% beryllium. In the USA Bertrandite Ore (3Be0 Al2O3 6SiO2) is mined from
a deposit in Utah, where it occurs close to the surface and can be
extracted in an environmentally friendly method. The earth that is
removed to expose the thin deposits of Bertrandite are carefully stored
and replaced in exactly the same location from where they were
removed after the Bertrandite layer has been removed. Modern GPS
surveying allows for accuracy within 1”, and the mine owned and
operated by Materion Brush Resources Inc. receives ongoing recognition
from the environmental community for its efforts to pursue sustainable
mining operations that do not harm the fragile desert ecosystems or
animal and human neighbors.
​
A small fraction of beryllium is obtained from Beryl (Be4 Si2O7 (OH)2 ),
a by-product of small scale emerald gemstone mining operations in
Brazil, Argentina and other countries in South America. That material
contains between 3.0 – 5.0% beryllium, but it is much harder than
Bertrandite, and so is more difficult to refine to beryllium. Before it can be refined, it must be melted in an electric furnace, and the molten material is dropped into a large pool of water which breaks it up into a fine powdery state called “frit”, which can be chemically processed with the Bertrandite ores.
​
-
Beryl ore is melted in industrial furnaces, solidified and crushed, then treated with sulfuric acid to produce a water-soluble sulfate.
-
Bertrandite ore is crushed, made into slurry and treated with sulfuric acid to form a sulfate.
-
The sulfate solutions undergo a series of chemical extraction steps to ultimately produce extremely pure berylliumhydroxide, from which virtually all contaminants have been removed.
-
Beryllium hydroxide Be(OH)2 is the common input material for copper beryllium alloys, beryllia ceramics and pure beryllium metal manufacturing.
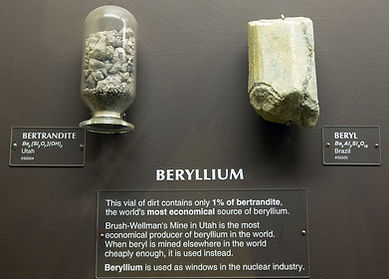
CONVERTING BERYLLIUM
CONTAINING MINERALS INTO BERYLLIUM HYDROXIDE
-
The mined ore is crushed in a ball mill, a big cylindrical drum that contains hard steel or ceramic balls and is rotated sothat the balls continuously impact the pieces of ore and gradually produce a fine powder with about the grain size of beach sand
​
-
The crushed ore is mixed with Sulfuric acid, which dissolves the beryllium, along with some other naturally occurring metals that are contained in the ore, and the solution containing the metals is stored in a large tank.
​
-
The metal containing solution is diluted with water and pumped into another series of tanks that contains an organic liquid that does not mix with water. The beryllium concentrates in the organic fraction and the water based fraction is left with a higher concentration of the aluminum, iron and other metals that were in the original ore. This “solvent extraction” process is repeated many times, through the series of tanks until the beryllium is free of other harmful metal elements.
​
-
The final concentrated organic fraction is treated with ammonium carbonate solution, which precipitates pure beryllium hydroxide Be(OH)2 when heated up slightly.
​
-
The beryllium hydroxide is washed and dried to produce the universal raw material from which all other forms of beryllium are made. When dried out by heating to a high temperature the water molecules in the beryllium hydroxide are removed, leaving pure beryllium oxide (BeO).
CONVERTING BERYLLIUM HYDROXIDE
INTO USABLE FORMS OF BERYLLIUM
Beryllium Metal
-
This is made by first forming Beryllium Fluoride from the beryllium oxide. This cannot be done directly by an aqueous route, so the hydroxide is first dissolved in ammonium bifluoride solution, and ammonium fluoroberyllate is precipitatedout. That material is subsequently heated to a high temperature over 900 degrees C to produce molten beryllium fluoride, that is then cast in molds into solid form.
​
-
The beryllium fluoride is then mixed with molten magnesium in large carbon containers, called crucibles, and the resulting molten liquid comprised of slag plus beryllium metal material is cast into a cold mold. When solidified, there are spherical balls of fairly pure beryllium with a beryllium content over 97% called pebbles contained within a glassy solid slag that can be readily separated and the pebbles collected.
​
-
The pebbles are further purified by melting them in a vacuum furnace, in which the vacuum allows any magnesium impurity to boil off to be collected and recycled, and the remaining beryllium metal is thus refined to as high as 99.99% beryllium content.
​
-
In order to make solid shapes of beryllium metal, the material is usually made into a fine powder by various conventional powder metallurgy methods, in which the powder is compressed inside a polymer or metal “can” by cold or hot isostatic pressing and an extremely compact structure is formed that has minimal void content and optimum physical properties.
​
-
In order to manufacture the high beryllium alloys, typically containing between 40-60% beryllium, and a balance of aluminum, the appropriate portions of pure beryllium and aluminum are weighed out, mixed and placed in an electrical induction furnace in a vacuum chamber where they are melted and cast into the appropriate shapes. Alternatively, a higher integrity solid is manufactured by a powder metallurgical route as above, using an appropriatemixture of powdered beryllium and aluminum.
​
Copper Beryllium Alloys
a) Master Alloys, containing 3.5% beryllium:
-
All copper beryllium alloys are manufactured by first making a master alloy containing 3.5% – 10% beryllium in a copper matrix, to which other alloying elements are added and additional copper is added to make up the required alloy composition.
​
-
Beryllium hydroxide is added to pure copper and a source of carbon, such as graphite in an electric arc furnace and the carboxythermic reaction results in a stochiometric alloy composition of copper with 3.5% beryllium contained. This is cast into molds to produce 10 – 20 lb solid ingots, referred to as copper beryllium master alloy.
​
-
Virtually all of the waste products generated as furnace drosses, slag, manufacturing process scrap and post consumer scrap is recovered and recycled through the arc furnace as a valuable source of beryllium. It requires less than half the energy to recycle beryllium compared to mining it from the earth, and avoids the use of process chemicals such as sulfuric acid and ammonia, thereby both protecting the environment and reducing the cost of producing beryllium.
​
b) Master Alloys, containing 3.5% beryllium:
-
Copper beryllium master alloy is melted in an electrical induction furnace with additional copper and some critical alloying elements such as nickel and cobalt to produce a range of alloy compositions containing between 0.3 – 2.0% beryllium. By varying the composition, a controlled range of physical and mechanical properties can be obtained.
​
-
The molten metal alloys are poured into vertical water cooled molds, from which the solidified alloy can be pulled through the lower end, so that a strand of solid metal can be continuously cast to produce the desired length of solid alloy. Typically strands are cast with cross sections from 2” – 30” in round, square and rectangular shapes, depending upon the final desired shape of the materials.
​
-
The continuously cast strands, cut into convenient lengths are then heated to an appropriate temperature to soften the metals, and then hot rolled, extruded or forged to an intermediate size.
​
-
Further cold forming such as rolling to thinner gauge strip products, forging or drawing to rod, wire or tube is carried outin conjunction with heat treating. This critical metallurgical process involves heating the solid alloy up to a carefully controlled temperature at which the alloying elements diffuse in the solid copper matrix to form specific alloy phases, or crystalline forms. This is then quickly cooled, or quenched, to a suitably low temperature to prevent the dissolved elements from escaping out of the crystalline structure that they had at the higher temperatures. This physical state is referred to as “solution annealed”, and the material is relatively soft and ductile, readily allowing further deformation and shaping to be carried out.
​
-
To obtain specific physical properties, the solution annealed material can be hardened by two complimentary methods which alone, or in combination provide a powerful control mechanism to obtain the desired combination of properties:
​
-
Work Hardening: In this process, additional reduction in size results in the uniform geometrical crystalline structure of the alloy being scrambled into random, broken up sections of crystalline structure, divided by “dislocations”. These dislocations prevent the smooth sliding of layers of crystalline structure, and hence strengthen the metal.
-
​Heat Treatment: If the solution hardened material is subsequently taken up to a temperature below the solution treatment temperature, atoms of the dissolved alloying elements are made more mobile, and can diffuse across the copper matrix structure to collect together into small clusters, or “precipitates”, of specific composition. The number and size of the precipitates can be controlled by the time and temperature of the heat treatment. Like the dislocations of work hardening above, the precipitates prevent the smooth sliding of layers of crystalline structure, and hence strengthen the metal. In addition, the influence of removing atoms of alloying elements from the copper matrix can change other properties such as the electrical and thermal conductivity.​
Heat treatment can be carried out by the copper beryllium manufacturer to deliver a product that can be finished by
a user to the desired shape. In other cases, it is more convenient for further forming operations such as machining and
stamping to be carried out by a component manufacturer to produce a finished product shape prior to heat
treatment to obtain the required set of properties.